Safety Field Guide
The Field Guide provides safety guidelines/tools for the NC State Facilities Division. Consult this guide before performing potentially hazardous work. The Field Guide is not all-inclusive. Before performing tasks, consult your supervisor, Standard Operating Procedures (SOPs) or Facilities Division safety professionals for specific safety guidelines. Make safety a part of everything you do – for your safety and for the safety of those around you.
Facilities Safety Professional:
Brian Carter, (919) 515-9820
Table Of Contents
Getting Started
Introduction
Communication
How To Report A Hazard
How To Report A Mishap
Training
Safety Committee
Position Responsibilities
Glossary
Hazard ID & Mitigation
The Process
Mechanical
Electrical
Pressure
Health
Ergonomics
Struck By or Against
Temperature
Vehicles
Slip/Trip/Fall
Chemical
Infectious Disease
Specific Tasks & Hazards
Bloodborne Pathogens
Communications
Confined Space
Electrical Safety
Emergency Reporting
Ergonomics
Fall Protection
Hand and Power Tools
Hazard Communication (Hazcom)
Heat/Cold Illness Protection
Hot Work (Flame Arc Spark)
Job Hazard Analysis
Ladder Safety
Lock Out Tag Out
Machine Guarding
Material Handling and Rigging
Mobile Equipment and Spotters
Office Safety
PPE and PPE Hazard Assessment
Sign, Tags and Barricades
Trenching and Excavation
Vehicle Safety
Work On Or Near Public Roadways
Working Alone Policy
General Information
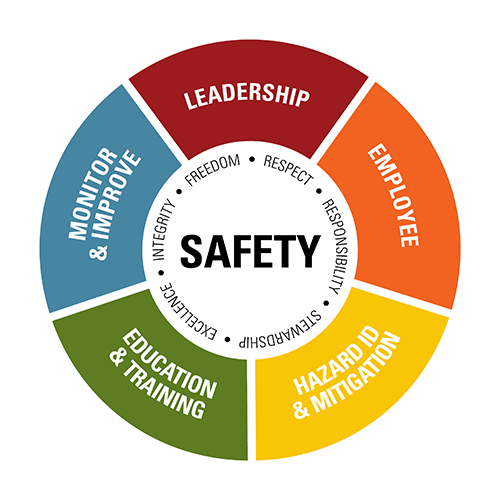
At the center of everything we do are NC State’s core values: freedom, respect, responsibility, stewardship, excellence and integrity. In addition, our Safety Management System includes five categories: Leadership, Employees, Hazard ID and Mitigation, Education and Training, Monitoring and Improvement.
This Safety Field Guide has been developed as a tool to help ensure your safety. It can, in no way, replace the situational awareness and safety achieved by using the Hazard ID and Mitigation Process. The process helps systematically identify hazards and how to mitigate those hazards.
The Facilities Division is committed to creating a safety culture where everyone is responsible for ensuring a safe workplace. Only through your personal commitment to this safety mindset will we achieve a workplace where no one gets hurt.
Your willingness to follow the safety practices outlined in this guide is vital to preventing mishaps on campus. Through this guide and other NC State safety educational resources, you will be able to identify hazards and respond.
Core Value | What It Looks Like |
Freedom | Unrestricted collaboration in sharing ideas/concerns that could prevent mishaps. |
Respect | Respect the contributions of each employee to a safe workplace. |
Responsibility | All employees are responsible for the safety of themselves and coworkers. |
Stewardship | Be intentional in the care for each other and the university community. |
Excellence | Put safety at the forefront of all decisions so no mishaps occur. |
Integrity | Do your job the safe and right way every time – even when no one is watching. |
Mishap prevention relies on the exchange and enhancement of knowledge. To assist with this, you will need to communicate about safe work methods, requirements and procedures. With any topic, it is most effective to divide your presentation into sections.
- Name the activity.
- What are the hazards?
- What are the controls?
- Implement controls.
- How do we continue to monitor whether controls are effective? What should we do if conditions changes?
A hazard is any object, situation or behavior that has potential to cause injury, illness or damage to property or the environment. When you see a hazard, immediately report it as follows:
Emergencies: Call 911
Examples: Crime, fire, serious vehicle collision, medical emergency, hazardous material spill, downed electrical wires, etc.
Non-Emergencies:
- If within your ability to immediately correct, take measures to mitigate the hazard. (Example: an empty box was left in a hallway where someone could trip over it; move it out of the walkway).
- If in your immediate work area and not within your ability to immediately correct, take measures to keep others from being injured and notify your supervisor (Example: Valve handle is damaged. Apply a “Do Not Use” tag and notify supervisor).
- If not in your immediate work area and not within your ability to immediately correct, take measures to keep others from being injured and notify your supervisor OR contact the Customer Service Center at 919-515-2991 (Example: Missing manhole cover. Barricade area or stay at location to help pedestrians avoid the hazard and call the Customer Service Center to dispatch personnel to respond.).
Reporting is critical to improving safety management and preventing incident recurrence. Employees must report all incidents to their supervisor – immediately – even if no injury occurred.
Critical Numbers:
- Emergencies: Dial 911
- Urgent facility repairs: Dial 919-515-2991
If the mishap results in injury:
- Call 911 for urgent medical attention.
- Notify supervisor.
- If an employee needs non-urgent medical treatment, the supervisor will arrange transportation to a medical provider.
- If an employee sees a medical provider as a result of a work-related injury, the supervisor must notify (within 24 hours of the incident) the respective unit director. The unit director or senior director will notify the Facilities Division Associate Vice Chancellor. This reporting enables collaboration at all levels of the Division to prevent recurrence.
- Supervisor ensures employee completes the Employee Statement Form.
- Supervisor submits all forms within 24 hours to Facilities Safety, Facilities Human Resources, Environmental Health and Safety, and Worker’s Compensation.
If the mishap does not result in injury:
- Notify supervisor.
- Supervisor ensures employee completes the Employee Statement Form, if required
- Supervisor submits all forms within 24 hours to Facilities Safety, Facilities Human Resources, Environmental Health and Safety, and Worker’s Compensation.
Education and training are important tools for informing workers and managers about workplace hazards and controls. This enables all employees to work more safely and be more productive.
Another role of education and training is to provide a greater understanding of the safety and health program itself so that employees can contribute to its development and implementation. Education and training provides employers, managers, supervisors, and workers with:
- Knowledge and skills needed to do their work safely and avoid creating hazards that could place themselves or others at risk.
- Awareness and understanding of hazards and how to identify, report and control them.
- Specialized training when their work involves unique hazards.
Additional training may be needed depending on the roles assigned to employers or individual managers, supervisors and workers.
Effective training and education can be provided outside a formal classroom setting. Peer-to-peer training, on-the-job training and on-site demonstrations can be effective.
Resource: Facilities Division Safety Training Plan
The Facilities Safety Action Committee gives a voice to all Facilities employees. This ensures that the Facilities Division identifies and implements solutions that are the most effective. The purpose of the Safety Action Committee is to establish and sustain an effective safety culture and climate
Safety culture encompasses “the deeply held, but often unspoken, safety-related beliefs, attitudes, and values that interact with an organization’s systems, practices, people, and leadership to establish norms about how thing are done in the organization.” Safety climate, on the other hand, comprises “the shared perceptions of safety policies and procedures by members of an organization at a given point in time.” A good safety climate can be promoted by staff commitment to safety, realist practices for handling hazards, continuous organizational learning, and care and concern for hazards shared across the workforce.
Contact the committee to report a safety concern.
Supervisor
Supervisors play a key role with very specific health and safety responsibilities. A supervisor is a person who instructs, directs and controls workers in the performance of their duties. A supervisor can be any worker — management or staff — who meets this definition, whether or not he or she has the title of supervisor. Supervisor responsibilities associated with day-to-day operations include:
- Defining safety expectations relevant to the scope of work being performed in general and specific to each task. Confirm expectations are understood
- Ensuring employees are properly trained and competent to perform assigned tasks.
- Providing the necessary resources to perform tasks safely.
- Monitoring (periodically) the work to ensure it is being performed according to defined expectations.
- Providing feedback before, during and after tasks, focusing on positive employee actions and coaching when unsafe conditions or at-risk actions are observed.
Additional supervisor responsibilities relevant to specific activities are provided in this field guide and within Facilities Division and university safety procedures (i.e. conduct safety meetings, mishap review, fall protection, confined space, etc.).
Employee Rights and Responsibilities
Rights
- Participate in the safety and health program.
- Be trained in hazard recognition and safe work practices.
- Be informed of unsafe or unhealthful conditions.
- Refuse to work if imminent danger exists or if it is believed to exist.
- Be free from reprisal or retaliation by a supervisor or other manager because personnel exercised any right under the Occupational Safety and Health Administration (OSHA), such as reporting unsafe conditions, mishaps or injuries.
- Be provided all required PPE to perform work tasks safely.
Responsibilities
- Report any known or potential hazards.
- Follow safety rules and use safe work practices so employees do not endanger themselves or their co-workers, or infringe upon the rights of other workers.
- Use protective clothing or equipment, when required.
- Attend scheduled safety and occupational health-related training.
- Actively look for and report unsafe or unhealthful conditions that pose a hazard to themselves or others.
- Report mishaps, injuries, illnesses and near misses to their supervisor immediately.
Hazard Identification and Mitigation
Step 1: Identify Hazards
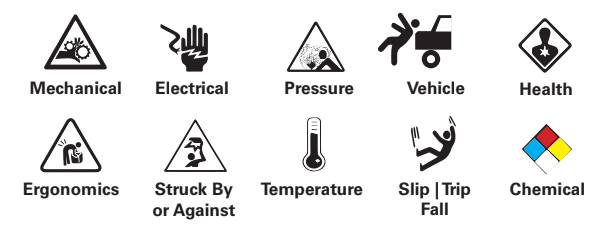
Step 2: Assess Hazards
Evaluate: How could the hazards affect safe completion of the job?
Step 3: Establish Controls
Use the hierarchy of controls.
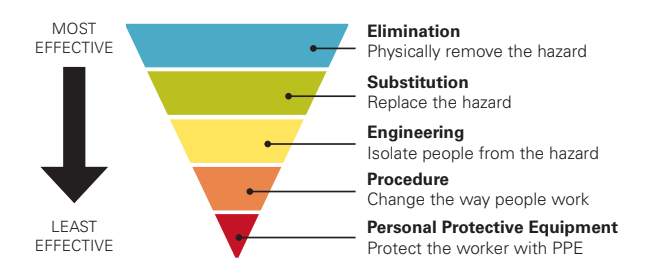
If you are unsure how to control a hazard, PAUSE and talk to your supervisor.
Step 4: Monitor Effectiveness
Verify that controls are effective for the entire duration of the job.
- Read the manufacturer’s instructions on how to operate the machine safely and correctly.
- Always be sure that moving mechanisms are clear of people and objects.
- Be sure that workers are not wearing any jewelry or loose clothing that could get snagged in the machine.
- Keep an eye on overhead moving parts, like pulleys, for potential hazards.
- Check that guards are in place at all points where you could contact moving parts before turning the machine on.
- Be aware of how to turn power on and off if you should have to do so quickly.
- Feed material into the machine with push sticks, not your hands.
- Pause. Rushing through a job is one of the major causes of accidents.
- Make sure maintenance is performed when required. If you think your equipment might have missed its scheduled maintenance let your supervisor know.
- Use lock out/tag out procedures when a machine needs repair or maintenance. Turn the machine and the power to the machine off and tag it so that no one tries to use it.
- Assume that all overhead and underground wires are energized at lethal voltages. Never assume that a wire is safe to touch even if it is down or appears to be insulated.
- Never touch a fallen overhead power line. Call 911 or the electric utility company to report fallen electrical lines.
- Stay at least 10 feet (3 meters) away from overhead wires during cleanup and other activities. If working at heights or handling long objects, survey the area before starting work for the presence of overhead wires.
- Always inspect electrical components of tools and equipment for damage before operation. Tag damaged equipment with a “Do Not Operate” tag.
- Never operate electrical equipment while you are wet or standing in water.
- Never repair electrical cords or equipment unless qualified and authorized.
- If working in damp locations, inspect electric cords and equipment to ensure that they are in good condition and free of defects, and use a ground-fault circuit interrupter (GFCI).
- Energized work is only permitted by qualified electrical workers and only under very specific circumstances as specified in the Energized Electrical Work Policy.
Pressure is continuous physical force exerted on or against an object by something in contact with it. Never assume that a pressurized system is depressurized.
- Always evaluate surroundings for conditions that may present pressure hazards. Some things to look for: piping systems, particularly those with pressure gauges; cables, ropes, chains in a taut condition; compressed gas cylinders; hydraulic systems and piping; tree branches bent over from snow or ice.
- When working around pressurized systems, equipment or objects, avoid the “line of fire” (the expected path of uncontrolled energy).
- Place barricades to prevent access to areas containing hazardous pressure sources.
- Use appropriate personal protective equipment when working with pressurized systems.
Steam Safety
Working safely with steam systems involves properly selected equipment, regular equipment inspection and maintenance, safe work procedures, PPE and employee training. The steam lines located in the central utility plants, mechanical rooms and in the steam tunnels are under a tremendous amount of pressure. Steam is particularly hazardous due to its high pressure and temperature (as high as 150psi and 366°F). If a person were to be in the line of fire, severe injury is certain.
Compressed Gas Cylinders
Cylinders must be secured to prevent tip over when in use, transported, moved or stored. When stored, flammables and oxygen must be separated by a ½ hour fire-rated wall or by 20 feet. Valve protection caps must be in place before transported, moved or stored.
In order to mitigate health hazards associated with occupational exposure to hazardous substances and conditions, the following programs are active within the Division.
- Asbestos Management Plan: For materials containing more than one percent (>1%) asbestos.
- Chemical Exposure Prevention and Hazard Communication: Measures to prevent employee exposure to hazardous chemicals include the use of proper engineering controls, work practices and protective equipment.
- Hearing Conservation Program: When engineering and administrative controls are not successful in lowering noise exposure, hearing protection devices must be used. Employees exposed to operations where noise levels are 85 dBA as an 8-hour time-weighted average or more must be covered under the hearing conservation program.
- Medical Surveillance: This may be recommended or required based on the type of work being performed, including factors such as the duration of the task, the materials being used and the potential for exposure.
- Respiratory Protection: Employees who wear a respirator must be given prior approval by EHS. Before a respirator is issued, a workplace assessment is conducted to identify harmful airborne chemicals.
- Silica Exposure Control Plan: Operations involving exposure to respirable crystalline silica must be covered under the plan, which details the methods for controlling exposure for specific tasks. Examples of covered operations: cutting, grinding, drilling or crushing brick, block, concrete, stone, rock, mortar and other materials that contain crystalline silica.
By removing the risk factors that lead to injuries, you maximize safe work performance and ensure employees perform their jobs within their body’s capabilities and limitations. The primary workplace ergonomic risk factors are:
- High Task Repetition: Many work tasks and cycles are repetitive in nature and frequently controlled by hourly or daily production targets and work processes. High task repetition, when combined with other risks factors such high force and/or awkward postures, can contribute to the formation of musculoskeletal disorders.
- Forceful Exertions: Many work tasks require high force loads on the human body. Muscle effort increases in response to high force requirements, increasing associated fatigue which can lead to musculoskeletal disorders.
- Repetitive/Sustained Awkward Postures: Awkward postures place excessive force on joints and overload the muscles and tendons around the affected joint. Avoid reaching, twisting, and bending, keep the torso in a neutral posture with shoulders in line with hips and feet. Keep arms close to the body. Use reach assist tools and step stools. Break tasks into steps to avoid twisting and bending.
Ergonomic Evaluation
University employees can request an ergonomic evaluation, ergonomic training, workstation evaluation or a risk assessment survey from Environmental Health and Safety (EHS). This evaluation will provide the following services:
- Perform on-site and online evaluation of employee’s workstations.
- Recommend ways to minimize or control ergonomic stressors.
- Provide training/information about ergonomics, as well as product information.
Resources: Additional Information
Struck-by or against injuries result from forcible contact or impact between a person and an object or piece of equipment.
Secure Objects and Equipment
- When assembling or disassembling equipment, furniture, etc., ensure there are no loose objects or materials that could fall uncontrolled.
- Remove or secure items that could swing or fall from loads being lifted or moved.
Install Barricades
This prevents access to areas in which falling objects are anticipated. Barricade and/or use a spotter to prevent employees from walking under an aerial lift, below scaffold work platforms or below employees working on ladders.
Power Tool Safety
- Ensure guards are on power tools and equipment that generate flying objects (grinders, saws, drills, etc.)
- Wear appropriate personal protective equipment when using hand and power tools.
- Secure workpiece in a vise or other method.
Safe Work Area
- Ensure materials are properly stored in designated areas on appropriate racks and piles. Do not lean materials against walls or place on floor where they could pose a tripping hazard.
- Observe the work area for protrusions or obstructions in the walkways or working area (i.e. low hanging pipes, support beams, etc.). Apply padding or highly visible markings.
- Ensure walkways and work areas are adequately illuminated.
- Ensure vehicles and mobile equipment are secured when parked to prevent unintentional movement: parking brake, wheel chocks.
Heat-Related Illness
Heat-related illness is preventable. Workers who have not spent time recently in warm environments and/or been physically active will need time to build tolerance to the heat.
- Supervisors should encourage employees to consume adequate fluids (water and sport drinks), take frequent breaks and quickly identify heat illness symptoms.
- Other options for keeping body temperatures down include making changes to workload and schedules. For example, slow down physical activity by reducing manual handling speeds, scheduling work for the morning or shorter shifts with frequent rest breaks in the shade or away from heat sources.
Cold-Related Illness
In cold temperatures, your body loses heat faster than it can produce heat. Prolonged exposure to cold will eventually use up your body’s stored energy, resulting in hypothermia (abnormally low body temperature). Hypothermia can also occur at temperatures above 40°F if a person becomes chilled from rain, sweat or submersion in cold water.
- Be sure the outer layer of your clothing is tightly woven and preferably wind resistant. Wool, silk or polypropylene inner layers of clothing will hold more body heat than cotton.
- Stay dry. Wet clothing chills the body rapidly. Excess perspiration will increase heat loss, so remove extra layers of clothing whenever you feel too warm.
- Do not ignore shivering. It is an important first sign that the body is losing heat. Persistent shivering is a signal to return indoors.
Thermal Hazards
Precautions such as shielding and/or PPE are necessary for tasks and operations that generate or involve exposure to very high or low temperature objects, materials and surfaces. Examples include, hot surfaces following welding, cutting or soldering; working with cryogenic liquids (i.e. liquid nitrogen); etc. Signs should be posted to warn others of thermal contact hazards.
Hot Work
Hot work – jobs that involve burning, welding, grinding, or using fire or spark-producing tools – can result in fires, explosions and burn injuries. Perform hot work in safe locations away from fire hazards; never perform hot work in an area where flammable vapors or combustible materials exist, and add appropriate PPE as required for the work task. Use guards to confine the heat/sparks/slag and to protect immovable fire hazards. Ensure appropriate fire-extinguishing equipment is on hand in case of emergency. IMPORTANT: To obtain a “hot work permit” between normal operating hours (Mon – Fri, 8 am – 5 pm) call (919) 515-2568. If no answer, call (919) 515-3000.
Stay Safe
- The driver and passengers should wear a seat belt at all times.
- Be well-rested before driving.
- Avoid medications that cause drowsiness.
- If you are impaired by alcohol or any drug, do not drive.
Stay Focused
- Driving requires your full attention. Avoid distractions, such as adjusting the radio or other controls, eating or drinking, and phones.
- Continually search the roadway to be alert to situations requiring quick action.
- For long trips, stop about every two hours to stretch, walk and stay refreshed.
Avoid Aggressive Driving
- Keep your cool in traffic.
- Be patient and courteous to other drivers.
- Do not take other drivers’ actions personally.
- Reduce your stress by planning your route ahead of time (bring the maps and directions), allowing plenty of travel time, and avoiding crowded roadways and busy driving times.
Backing Vehicles
- When possible avoid the need to back vehicles by parking in a manner to allow the first move to be forward.
- When a second person is available, use them as a spotter. When alone, drivers should get out and look before backing.
Slips, trips and same level falls can occur anytime. To help prevent potential accidents and injuries:
- Wear proper footwear that is appropriate for the conditions. On smooth or wet surfaces, always wear shoes with slip resistant soles.
- Slow down, shorten your stride and use caution when walking on wet or slippery surfaces.
- Poor lighting can impair vision and increase the likelihood of slipping, tripping and falling.
- Report non-functioning lights, as well as walkways and work areas that are too dark.
- Be alert for uneven surfaces (potholes, speed bumps, platforms, doorways, cover plates, soft patches, curbs and elevator thresholds, etc.).
- Don’t leave loose objects on walking surfaces, working surfaces or stairways.
- Never leave water or oil spills unattended. If they can’t be cleaned up immediately, set up a barrier so that people know about the hazard.
- Always use a ladder or step stool. Never stand on a chair, desk, shelf, crate, box or any other unstable items to reach something. If you must routinely reach items in high locations, purchase a ladder or step stool.
- Report or repair loose or damaged handrails, stairway treads, mats and walkway runners. Even a small worn spot can cause a trip.
- When walking, don’t carry loads that block your vision. If you can’t see where you are going, a trip and fall is inevitable.
- Post signs to warn of hazardous areas. For example, paint edges where elevation changes occur with yellow paint to alert of the change in elevation; place ‘wet floor’ signs.
- Use handrails in stairways to avoid falls.
- Report any unprotected floor openings. These openings can cause very serious falls.
Working at Heights
Employees shall be protected with a passive or active fall protection system when working at a height of 4 feet or greater from the surface below. Keep away from the edge of unprotected roofs and elevated floors.
When people think of chemicals, it often evokes images of laboratories. But, in reality, chemicals are also found in many of the products we use at home and at work. While they have a variety of beneficial uses, chemicals can also be extremely hazardous if misused or mishandled.
OSHA’s Hazard Communication Standard (HCS) defines a hazardous chemical as “any chemical which can cause a physical or a health hazard.” With so many hazardous substances at work, it’s important to know how to identify common workplace chemical hazards – and how to avoid them.
Employers with hazardous substances must include warning labels and Safety Data Sheets (SDS) with their products as chemical hazards and toxic substances can present a wide range of short- and long-term health issues, including poisoning, skin rashes and disorders of the lung, kidney and liver.
Information about the identities and hazards of chemicals must be available and understandable to workers. The OSHA HCS is designed to ensure that information about chemical and toxic substance hazards in the workplace and associated protective measures is disseminated to workers.
If you are unsure of the identity, proper use, or hazards of a chemical, stop and ask your supervisor before using it.
Infection Control Basics
Infectious agents include bacteria, viruses and other microbes (i.e. germs). Most of these agents don’t harm humans, but some can cause disease ranging from mild to severe, even life-threatening.
There is a difference between infection and disease. Infection occurs when an infectious agent enters a human body and begins to multiply. Disease occurs when the cells in your body are damaged as a result of the infection and signs and symptoms of illness appear.
In response to infection, the body’s immune system acts to fight the infection, which may result in fever, coughing, sneezing, etc. to either kill the infectious agent or expel it from the body.
Infection Prevention
Methods to Avoid Infections
- Understand how infections can spread person to person. Infectious agents may be transmitted from person to person when an infected person’s respiratory droplets travel through the air and these droplets land in the mouths, noses or eyes of another person nearby, or the droplets are inhaled into the lungs. It can also happen when a person touches an object or person that has the infectious agent on it or them, then touches their mouth, nose or eyes.
- Wash hands often to protect against most infections. Wash hands thoroughly (for at least 20 seconds) before preparing or eating food, after coughing or sneezing, after using the bathroom, caring for someone who is sick, after in public when contacting frequently touched items or surfaces, etc. When soap and water aren’t available, alcohol-based hand-sanitizing gels (at least 60% alcohol) should be used.
- People who are sick must stay away from others. The best way to avoid spreading infection is for symptomatic people to avoid public places, including the workplace. Stay at least 6 feet away from another person who exhibits symptoms.
- Cover mouth and nose with a tissue or inside of the elbow when coughing or sneezing. Immediately throw tissues in the trash and wash hands.
- Clean and disinfect surfaces, particularly frequently touched surfaces. Also clean surfaces of shared tools, equipment and vehicles.
During an outbreak, epidemic or pandemic, enhanced prevention methods must be implemented. These may include:
- Procedures for prompt identification and isolation of sick people
- Procedures for flexible work schedules and remote working
- Engineering controls: HVAC adjustments and filtration, physical barriers, etc.
- Administrative controls: modified shifts and schedules, increased hand washing, stay at home orders, working remotely, modify work practices
- Personal Protective Equipment: respirators, masks, gloves, eye protection, etc.
Specific Tasks Or Hazards
What are bloodborne pathogens?
Bloodborne pathogens are infectious microorganisms in human blood that can cause disease in humans. These pathogens include, but are not limited to, hepatitis B (HBV), hepatitis C (HCV) and human immunodeficiency virus (HIV). Needlesticks and other sharps-related injuries may expose workers to bloodborne pathogens.
How can employees protect themselves?
All employees must be trained on and implement the concept of Universal Precautions. Employees with ‘occupational exposure’ are required to be covered under an exposure control plan. Universal Precautions is an approach to infection control in which all human blood and certain body fluids are treated as if known to be infectious.
Exposure Control Plan
Divisional units with employees that have occupational exposure to bloodborne pathogens are required to have a site-specific Exposure Control Plan, which is a written document that includes exposure determination, methods of compliance, hepatitis B vaccination, post-exposure evaluation, communication of hazards and recordkeeping.
Resources: Environmental Health and Safety
A two-way radio is a critical communications tool for safety. Basic training can make the difference between efficient and timely communications and response – and a complete communications breakdown between staff. New employees should always be coached in the protocols that specifically apply to your operational set up. Their safety and security in the workplace, and that of colleagues, will depend upon this. Here are some basic radio communication guidelines that could prove useful:
Perform radio checks
- Before using, ensure your radio battery is charged and power is on.
- Keep volume high enough to hear calls.
- Make regular radio checks to ensure everything is working and you are still in range.
Prepare before you speak
- Decide what you are going to say and who your message is meant for.
- Identify yourself before you talk – memorize call signs and use yours before speaking.
- Channels are shared. Don’t transmit sensitive or confidential information unless you are sure it is appropriate.
- Speak slowly and clearly.
- Say “over” to indicate you are finished so the other party know they can speak or reply.
Keep it simple
- Avoid long, complicated sentences. Be precise and to the point.
- Don’t use abbreviations unless these are well understood by your group.
- Terminate the call by saying “out.”
Stay on point
- The radio is for sending and receiving important messages – not for gossip/small talk that blocks channels for other radio users.
- Do not interrupt others when they are speaking; wait patiently until they finish.
- Use the Phonetic Alphabet to spell out key words: Alpha, Bravo, Charlie, Delta, Echo, Foxtrot, Golf, Hotel, India, Juliet, Kilo, Lima, Mike, November, Oscar, Papa, Quebec, Romeo, Sierra, Tango, Uniform, Victor, Whiskey, X-ray, Yankee, Zulu.
IMPORTANT: No permit-required confined space entry operations may be performed without the issuance of a Confined Space Entry Permit. The permit requirements must be followed at all times.
A confined space is a space that is large enough to bodily enter, has limited or restricted access/egress, and is not designed for continuous human occupancy. Common confined spaces can include (but are not limited to) sewers, manholes, tanks or vaults. All confined spaces must be evaluated prior to entry to determine if they meet the criteria that requires a permit for entry. Contact Facilities Safety for assistance.
Permit-Required Confined Space (PRCS)
PRCS has one or more of the following: hazardous atmosphere, potential for engulfment, potential for entrapment, or any other recognized safety or health hazard. There are three major roles/personnel positions involved with a PRCS:
- Attendant: Worker who remains outside the space at all times, prevents unauthorized entry, warns entrants of unusual conditions, performs non-entry rescue (i.e. tripod/winch) and notifies emergency rescue personnel if necessary.
- Entrant: Personnel required to enter the space to perform work.
- Entry Supervisor: Worker who coordinates entry into the space and completes the permit.
Permits to enter a PRCS are issued by the Entry Supervisor in accordance with the NC State Confined Space Entry Program. Confined space entry permits require certain information such as:
- Personnel involved in entry
- Emergency rescue services contacts
- Atmospheric monitoring information
- Ventilation requirements
- Communication procedures
- Other hazard controls (lock out tag out, blanking, blinding, double block and bleed, etc.)
Atmospheric Monitoring
Personnel performing air monitoring must be trained and knowledgeable of the equipment they are using. It is critical to ensure that air monitoring equipment is the correct equipment for the potential hazards, maintained properly and used correctly. The equipment manufacturer’s instructions must be followed (calibration interval of 30 days and daily bump test).
When it comes to confined spaces, correct procedure can be the difference between life and death. Don’t use equipment for which you have not been trained or appears to be working incorrectly.
Resources:
Confined Space
Confined Space Permit
Employees are not permitted to work on or near any exposed and energized electrical power circuit or parts unless such work is in accordance with the Facilities Division Standard Operating Procedure for Energized Electrical Work (i.e. SOP 835).
Electrical Safety Fundamentals
Electricity is safe when installed, maintained and used correctly. When not installed, maintained or used correctly, electricity is a serious workplace hazard that could result in electrical shock, burns, fire or explosions.
Electrical Shock
Electricity travels through completed circuits, takes the path of least resistance and seeks a path to ground. An electric shock can result in anything from a slight tingling sensation to immediate cardiac arrest. The severity depends on the following: the amount of current flowing through the body, the current’s path through the body, and the length of time the body remains in the circuit.
Precautions:
- Visually inspect electrical tools, cords, and equipment prior to use.
- Extension cords must be at least 12-gauge, 3-wire type and properly rated for the service. Do not use and dispose of, worn, frayed or damaged cords. Use cords with a ground prong. Cables passing through work areas must be covered or elevated to protect from damage and eliminate tripping hazard, and not attach to building or structure.
- Receptacles present near a water supply or outdoors must be protected with a Ground Fault Circuit Interrupter (GFCI) or use a portable GFCI when work may involve exposure to water or other conductive fluids.
- Ensure covers prevent exposed wires.
- Ensure lighting fixtures are in good condition with no exposed energized parts.
- De-energize and follow Lock Out Tag Out procedures when working with electrical equipment.
- Maintain adequate clearance distance from overhead energized lines and equipment.
Overhead Power Lines and Equipment
Any overhead utility will be considered to be energized unless and until the person owning or operating such line verifies that the line is not energized and the line is visibly grounded at the work site. No work near overhead utilities (i.e. power lines, communication lines, guy wires) will take place unless authorized through the utility owner in accordance with required safe work practices.
Equipment (for example, lifts with articulated upright booms, forklifts, excavators, etc.) are not permitted to operate within 10 feet of an overhead utility line with nominal voltage of less than 50kV while the boom is in the upright position. For lines in excess of 50kV, an additional distance of 4 inches for each 10 kV over 50kV will be maintained.
To report an emergency at NC State, always dial 911. Provide your full name and telephone number, as well as the nature and exact location of your emergency. Also provide clear details regarding the emergency, including number of injured people and nature of their injuries.
Chemical Spill
Call 911. Evacuate the area if necessary (use a fire alarm to evacuate the building if required).
Radioactive Materials
Call 911 and advise University Police to contact Radiation Safety. Isolate the area as needed.
Human Blood Spill
For assistance with injuries, call 911 from a campus phone or (919) 515-2991 for non-emergencies.
Fire Procedures
- Activate fire alarm pull station if in a building.
- Immediately leave the building – and if possible and safe – shut off equipment.
- Close your door to deprive the fire of oxygen.
- Alert others.
- DO NOT USE ELEVATORS.
- Call 911.
- Activate emergency blue light phone if nearby.
- Assemble in a predetermined safe place away from danger; account for coworkers.
- Person with knowledge of the situation should meet with first responders.
- Do not re-enter the building until cleared by first responders.
Other Important Numbers
Adverse weather and emergency conditions: (919) 513-8888
- Adverse Weather and emergency conditions: (919) 513-8888
- Environmental Health Safety: (919) 515-7915
- University Police non-emergency: (919) 515-3000
- Facilities Service Center: (919) 515-2991
- Student Health Services: (919) 515-2563
- Counseling Center: (919) 515-2423
- Women’s Center: (919) 515-2012
- Sexual Violence Helpline: (919) 515-4444
Ergonomics is a scientific discipline, which is concerned with improving the productivity, health, safety and comfort of people, as well as promoting effective interaction among people, technology and the environment in which both must operate.
Musculoskeletal disorders (MSDs) affect the muscles, nerves, blood vessels, ligaments and tendons. Workers in many different industries and occupations can be exposed to risk factors at work, such as lifting heavy items, bending, reaching overhead, pushing and pulling heavy loads, working in awkward body postures and performing the same or similar tasks repetitively. Exposure to these known risk factors for MSDs increases risk of injury.
Work-related MSDs can be prevented. Ergonomics — fitting a job to a person — helps lessen muscle fatigue, increase productivity and reduce the number and severity of work-related MSDs.
Proper Lifting
Stand as close to the item as possible. Bend with your legs, not your back to get beside the item. Estimate the item’s weight and dimensions. Observe this method to return an item. If at any time a load is too heavy or has the potential to be too heavy, PAUSE and ask for help and perform a team lift.
Avoiding Ergonomics Issues
- Stretch and walk around regularly; do not remain sedentary.
- Do not ignore pain. Inform your supervisor of ergonomic discomfort on the job.
- Avoid carrying items that are too heavy.
- Select tools that are ergonomically designed for comfort.
- Request an ergonomic evaluation of your area or work station.
Resources: Ergonomics
Fall Prevention And Protection
A fall hazard is any condition on a walking-working surface that exposes an employee to a risk of fall on the same level or to a lower level. Preventing falls on the same level requires keeping walking-working surfaces clear of slip and trip hazards. Preventing or protecting falls from height may be necessary at any height given the circumstances, but is required when an employee is at a height of 4 feet or more above a lower level.
The method of Fall Prevention or Protection utilized depends on the application: construction or general industry. Most facilities operations fall within general industry applications, where acceptable methods include a standard guardrail or personal fall protection system. When working on a low-slope roof (4:12 or less) the use of a Designated Area may be an option. Every employee required to work at unprotected heights (greater than 4 feet) are required to be trained in Fall Prevention.
Guardrail System
A guardrail system provides the highest level of protection and is always preferred. The system must be capable of supporting 200 lbs in any direction and still maintain its integrity. The individual heights of the components must conform to the following minimum standards:
- The top rail of the system must be at a height of 42” (+ or – 3”).
- The mid rail must be at a height of 21” with a 3” variation possible.
- The toe board must have a minimum vertical height of 3.5”.
There may be some variation in materials or design but these minimum standards are required. At times, it is necessary to work in areas where guardrails cannot be constructed; in these instances, a personal fall protection system must be used.
Personal Fall Protection Systems
Personal Fall Protection Systems are systems (including all components) that provide protection from falling or that safely arrest a fall. Examples include travel restraint and personal fall arrest. All components of this system shall meet the applicable design requirements as specified in OSHA 1910, 1926, or ANSI Z359. All components shall be inspected by the wearer prior to each use and at least annually by a competent person. No employee may use a personal fall protection system without proper training and an understanding of proper use and safe application of the system.
Travel Restraint System
A travel restraint system is a combination of an anchorage, anchorage connector, lanyard (or other means of connection) and body support that the wearer uses to eliminate the possibility of going over the edge of a walking-working surface. Anchorages for travel restraint systems shall have a strength capable of sustaining static loads of at least 5,000 lbs (per person) or two times the foreseeable forces for certified anchorages. Anchorage connectors, lanyards (or other means of connection) and body support devices shall be used in accordance with the manufacturer’s requirements. The system shall be installed so that a fall cannot occur; therefore, a rescue plan is not required.
Personal Fall Arrest System
A personal fall arrest system is a system used to safely arrest a user in a fall from a walking-working surface. It includes an anchorage, anchorage connector and a full body harness. The means of connection may include a lanyard, deceleration device, lifeline or a suitable combination of these. Equipment must be worn and used in accordance with the manufacturer’s requirements. Anchorages for personal fall arrest systems shall have a strength capable of sustaining static loads of at least 5,000 lbs (per person) or two times the maximum arresting force for certified anchorages. The system shall be installed so that should a fall occur, the wearer will not contact the lower level or any other obstruction. Since there is a potential for a fall to occur, a rescue plan written by a qualified person is required.
Designated Area
A Designated Area is a distinct portion of low-slope roof in which workers perform work and a standard guardrail or personal fall protection system is not required. Application of a designated area is only permitted as follows:
- Work is 15 feet or more from the edge. A warning line is installed and a work rule prohibiting workers from moving closer to the edge than 15 feet is established (warning line not required if work is both temporary and infrequent), OR
- Work is 6 – 15 feet from the edge, both infrequent and temporary, and a warning line is installed between the work and the edge but not closer than 6 feet to the edge.
- Infrequent: Typically monthly (or less frequent); a task or job performed only on occasion, when needed such as equipment break down.
- Temporary: No more than 2 hours.
- Warning Line: Rope, wire, chain or barricade erected on all sides of roof work area meeting requirements of 1910.29(d) – not less than 6 feet to edge, 200# tensile, 34-39” high, clearly visible at 25 feet, etc.
Resources: Fall Protection
Tool Safety
Except where more stringent requirements may exist, all hand and power tool operations shall be in accordance with OSHA 29 CFR 1910 Subpart P.
General
All hand and power tools shall be visually inspected prior to use for any defects. Tools with defects shall not be used and tagged out of service. Personnel shall only use tools for which they have been trained and in accordance with manufacturer requirements.
- Power tools shall not be used if safety equipment, such as shields, tool rests, hoods and guards have been removed or otherwise rendered inoperative.
- Employees using tools under conditions that expose them to risk of flying objects, harmful dust, and/or noise shall be provided with the required PPE.
- All electrically powered tools shall be properly grounded. Outlets for 110-volt tools shall be protected by ground fault circuit interruption devices whenever used in outdoor or wet environments and an assured grounding program shall be utilized. Double-insulated electrical hand tools are recommended.
- Positive locking or trigger lock devices are not allowed.
- Portable grinders will be provided with hood-type guards with side enclosures that cover the spindle and at least 50% of the wheel. All wheels will be inspected regularly for signs of fracture and that wheels are rated for the grinder’s RPM.
- Bench grinders shall have deflector shields and spindle cover guards. Grinders shall have a maximum of 1/4” clearance to top of the guard, and tool rests shall have a maximum clearance of 1/8” from the wheel. Bench grinders must be secured to the bench to prevent displacement of the unit during use. Whenever feasible, grinding wheels on all grinders should be removed prior to storage to prevent potential damage.
- Hoses supplying pneumatic tools shall have couplings secured to prevent accidental disconnection. “Push, twist, click” locking connection disconnects shall be used. Where those cam lock connectors are not used, a safety pin and whip check must be utilized. Quick disconnects larger than 3⁄4” inside diameter must have safety pins and whip cables attached to the hose, pipe connection and between connected hoses, unless automatic shutoff valves are used. Whip checks are required for air hoses 3⁄4” or larger.
- Air supply lines will be protected from damage, inspected regularly and maintained in good condition. Air sources supplying hoses exceeding 1/2”ID shall be protected by excess flow valves to prevent whipping in the event of hose separation or failure.
- The pressure of compressed air used for cleaning purposes will be reduced to 30 psi or less. Hose extensions will always be used. At no time shall compressed air be directed toward a person.
Powder-Actuated Tools
- Powder-Actuated tools should not be used on university property without prior approval.
Sharp Objects/Cutting Utensils
- Often field tasks require cutting of items such as rope, packaging or containers. Care should be exercised in using knives and/or cutting implements while performing cutting tasks.
- Personnel should use cut resistant gloves and cut down and away from their body and other personnel.
- The item being cut should be braced or secured from movement while cutting.
Manufacturer Guidelines
All manufacturers’ guidelines must be followed while using tools. This means that we cannot modify, change or otherwise use a tool in a way that it was not intended.
Inspections
Tools must be inspected before each use. The inspection for hand tools can include items such as broken, chipped or splintered handles, mushroomed heads or loose fitting parts. These defects must be fixed in the right way and not made worse by temporary inadequate methods. Any defects found during a visual inspection should be noted and the tool should be taken out of service. In addition, the electrical cords or air hoses on all power or air tools must be inspected before each use. These areas cannot be fixed with tape or other inadequate methods. All defects must be noted and the tool placed out of service.
Guarding
No tool equipped with a guard or protective device should be used without that guard in place and operational. Items like grinders, saws and some drills are considered unusable if the guard is broken, cracked or missing. Sometimes this means the tool itself should be discarded and in other cases it can be repaired. Always ensure a tool is either replaced or repaired instead of using any defective tools.
Resources: Hand and Portable Tools
“The Federal Right to Know Act” states that all employees have a right to know the specific health hazard information of any chemical they could potentially be exposed to as they work.
Training
All employees who work with any chemical that could create a potential hazard must be trained on the hazards and the best methods to prevent harmful exposure. This training must be provided and documented before starting the task that uses chemicals.
Container Labeling
All containers must be labeled, with the name of the contents, no symbols or abbreviations and the hazards. This includes materials that are transferred from a larger container to a smaller one, or secondary container for individual use. Never use a material from an unlabeled container. Secondary containers must be appropriate for the contents (i.e. no drink bottles).
Safety Data Sheets
Safety Data Sheets (SDS) of potentially harmful chemicals must be available for employees. These sheets are sent from the manufacturer and contain the name, properties, potential hazards and safety measures associated with the chemical. Every employee must be trained on the SDS for the chemical they are using and has the right to access these sheets at any time for clarification on potential hazards. If at any time a question arises ask a supervisor before working with any chemicals.
Heat Related Emergencies
There are stages or levels of heat related emergencies and corresponding treatments. Always take proper precautions, and never attempt to “work through” or allow others to work through these symptoms. Dial 911 for emergency assistance.
Heat stroke
Symptoms include confusion, fainting, seizures , very high body temperature and excessive sweating or red, hot, dry skin. Offer first aid:
- Place worker in shady, cool area.
- Loosen clothing; remove outer clothing.
- Fan air on worker; cold packs in armpits.
- Wet worker with cool water; apply ice packs, cool compresses, or ice if available.
- Provide fluids (preferably water).
- Stay with worker until help arrives.
Heat Exhaustion
Symptoms include cool, moist skin; heavy sweating; headache; nausea or vomiting; dizziness; lightheadedness; weakness; thirst; irritability or fast heart beat. Offer first aid:
- Have worker sit or lie down in a shady area.
- Provide water or other cool beverages.
- Cool worker with cold compresses/ice packs.
Heat Cramps
Symptoms include muscle spasms or pain usually in the abdomen, arms or legs . Offer first aid:
- Have worker rest in shady, cool area.
- Worker should drink water or a cool beverage.
- Wait a few hours before allowing worker to return to strenuous work.
- Seek medical attention if cramps persist.
Heat Rash
Symptoms include clusters of red bumps on skin that often appear on neck, upper chest or skin folds. Offer first aid:
- Work in a cooler, less humid location if possible.
- Keep the affected area dry.
Cold Illness
Cold temperatures and increased wind speed (wind chill) cause heat to leave the body more quickly, putting workers at risk of cold stress. Anyone working in the cold may be at risk. To protect yourself and others, know and monitor for the symptoms. Also, dress properly with layers of loose-fitting, insulating (and waterproof if necessary) clothes including jacket, gloves, hat and boots. Dial 911 in case of emergency.
Hypothermia
Normal body temperature (98.6°F) drops to 95°F or less. If mild, the person is alert but shivering. If moderate or severe, the shivering stops. There is confusion, slurred speech, slow heart rate and breathing, loss of consciousness or death. Call 911 immediately in an emergency. To prevent further heat loss:
- Move the worker to a warm place.
- Change to dry clothes.
- Cover the body (including head and neck) with blankets and with something to block the cold (e.g., tarp, garbage bag). Do not cover the face.
Frostbite
Frostbite occurs when body tissues, such as in the hands and feet, freeze. This can occur at temperatures above freezing – due to wind chill – and may result in amputation. Symptoms include numbness. Skin may appear reddened, with gray or white patches, feel firm or hard, and may blister.
- Follow the recommendations for hypothermia.
- Do not rub the frostbitten area.
- Avoid walking on frostbitten feet.
- Do not apply snow/water or break blisters.
- Loosely cover and protect areas from contact.
- Do not try to rewarm the area unless directed by medical personnel.
IMPORTANT: No hot work shall be performed without written approval and issuance of a Hot Work Permit. The requirements of the permit shall be followed at all times.
Except where more stringent requirements may exist, all hot work shall be in accordance with OSHA 29 CFR 1910 Subpart Q. Hot work is defined as any work that has the potential of creating or becoming a source of ignition. This includes grinding, welding, thermal or oxygen cutting or heating, and other related heat or spark-producing operations.
Hot Work Programs
The Hot Work Program is designed to minimize or eliminate fire hazards associated with any hot work operation as identified in the NC State Fire Code, OSHA 1910.252, NFPA 51B, NFPA 1962 and NC State University Department of Environmental Health and Safety / Fire and Life Safety’s Office Guidelines. This program applies to all contractors and university units conducting hot work on campus, such as welding, torching, soldering, cutting, brazing, grinding, use of tar kettles or other work that might create sufficient heat or spark that could start a fire.
Hot Work Permits for Cooking
A hot work permit is required for all grilling and frying done on campus. The University Fire and Life Safety Office issues annual hot work permits to NC State Housing to cover use of stationary grills. All grilling must be done outside and should be at least 25 feet from the building. You must possess a fire extinguisher before grilling and you may not remove an extinguisher that is mounted inside a building.
Permitting
To obtain a hot work permit between normal operating hours (Mon – Fri, 8 am – 5 pm) call (919) 515-2568. If no answer (or if it’s after hours, a weekend or holiday), call the communication center at (919) 515-3000. If you need to borrow a fire extinguisher, you may request one at that time.
A job hazard analysis (JHA) is a process that focuses on breaking down job tasks into a sequence of events, seeking out associated hazards and establishing controls to prevent mishaps. When performing a JHA, consider the relationship between the worker, the task, the tools and equipment, and the environment. The key is to involve everyone who will be participating in the job; employee involvement is essential. To perform a JHA, follow this simple process (or use the JHA Form):
Step 1. Breaking the job into steps
Before the search for potential hazards begins, the task is broken down into a sequence of events. Begin by asking, “What step starts the task?” Then, “What is the next basic step?” and so on. If more than 10 steps result from the analysis, consider breaking that job into more than one task.
Step 2. Identify possible hazards for each step
Once the basic steps have been determined, begin the search for potential and existing hazards. Look at physical conditions, environmental factors and actions or behaviors. The goal is to discover the following:
- What can go wrong?
- Who and what is at risk?
- What are the potential consequences?
Step 3. Preventative measures
The last step in a hazard analysis is to identify and implement control measures for each identified hazard. Some control measures may already exist and some may need to be put in place. Ask: “What can be done to eliminate or control each hazard?” If a hazard cannot be effectively eliminated or controlled, PAUSE and get others involved.
JHAs can be written or unwritten. Typically, low-risk tasks are unwritten and performed individually or through a small crew discussion at the start of a task. Tasks with greater risk and complexity require more detailed planning, which should be documented. Documenting the JHA helps to ensure that everyone involved understands what will happen, when and by whom. The written JHA can serve as the plan for executing the work in a manner that will prevent the occurrence of mishaps and as a training tool for new employees. Sometimes JHAs are built in as a part of other processes (for example: confined space entry or lock out tag out). When performing JHAs, refer to the Hazard Identification and Mitigation process.
Resources: JHA Form
Comply with ladder manufacturer requirements at all times. Before using a ladder, consider whether alternative methods (i.e. aerial lifts, scissor platforms, scaffolding, etc.) might provide a safer means to conduct work.
To prevent falls from ladders, make sure you have the following controls in place:
- Use only ladders that are in good condition and designed to handle the climbing job that needs to be done.
- Ensure employees are trained on proper ladder use.
- Complete an inspection before each use.
- Be sure step ladders are fully open and locked before climbing them. Do not climb any higher than the second step from the top (Tip: Your knees should be below the top cap).
- Place ladder on a flat, non-movable and secure surface.
- Place ladder on a hard surface as it will sink into a soft surface.
- Do not place ladder in front of a door.
- Face ladder when ascending or descending, and maintain 3-point contact.
- Carry tools in pockets, in a bag attached to a belt, or raised and lowered by rope.
- Work facing the ladder.
- Do not overreach, always keep your torso between the ladder rails.
Straight Ladders
- Lean ladder against a secure surface, not boxes or barrels.
- Use a 4:1 ratio for setting straight ladders; for every 4 feet in height at the resting point, the base should be moved out one foot.
- Ladder rails should extend at least 3 feet above top landing.
- Check shoes to ensure they are free of grease or mud.
- Mount the ladder from the center, not from the side.
- When climbing or working from a straight ladder, it must be secured by either tying it to the structure or having someone hold the ladder.
Lock Out Tag Out (LOTO)
LOTO refers to specific practices and procedures to safeguard workers from the unexpected energization or startup of machinery and equipment, or the release of hazardous energy while performing service or maintenance activities. LOTO involves eliminating or controlling energy sources using an energy isolating device and positively controlling those devices using a lock out device and/or tag out device. Note: Tag out devices alone may only be used in situations where it is not feasible to use a lock out device.
Key Terms
- Affected employee: An employee whose job requires him or her to operate or use a machine or equipment on which servicing or maintenance is being performed under lock out or tag out, or whose job requires him or her to work in an area in which such servicing or maintenance is being performed.
- Authorized employee: A person who locks out or tags out machines or equipment in order to perform servicing or maintenance on that machine or equipment. An affected employee becomes an authorized employee when that employee’s duties include performing servicing or maintenance.
- Energy Isolating Device: A mechanical device that physically prevents the transmission of energy, such as a manually operated electrical circuit breaker or disconnect switch, a line valve, bolted slip blind or blank flanges. Note: Push buttons, selector switches and other control circuit devices are not energy isolating devices.
- Lock Out Device: A device that uses a positive means such as a lock to hold an energy-isolating device in the safe position and prevent the energizing of a machine or equipment.
- Tag Out Device: A prominent warning device, such as a tag and a means of attachment, which can be securely fastened to an energy-isolating device in accordance with an established procedure, to indicate that the energy-isolating device and the equipment being controlled may not be operated until the tagout device is removed.
- Servicing and/or maintenance: Workplace activities such as constructing, installing, setting up, adjusting, inspecting, modifying and maintaining and/or servicing machines or equipment. These activities include lubricating, cleaning or unjamming machines or equipment and making adjustments or tool changes where the employee may be exposed to the unexpected energization or startup of the equipment or release of hazardous energy.
- Examples of hazardous energy sources: Electric, Pneumatic Pressure, Hydraulic Pressure, Thermal, Steam, Kinetic (motion), Compressed gas/air/liquid, Chemical, Radiation, Lasers, etc.
Who must follow LOTO?
Any unit with employees who perform servicing and/or maintenance activities must follow the energy control program.
Energy Control Program Requirements
- LOTO devices shall not be removed without following the steps listed in the energy control program.
- Every authorized employee shall work under the protection of LOTO.
- Each authorized person shall work under the protection of their own lock (i.e. ONE PERSON ONE LOCK).
- Energy control procedures are required for each machine or piece of equipment. Equipment that has more than one energy source must have written energy control procedures. Energy control procedures include specific procedural steps to shut down and isolate each energy source, safe LOTO device application, methods for verifying sources are deenergized, and procedural steps for placing the machine or equipment back into service.
- Affected and authorized employees shall be trained on the energy control program, which includes specific energy control procedures.
- Energy control procedures must be audited at least annually to ensure they are being followed.
Central Utility Plants: Any work involving the NC State Central Utility Plants shall follow the Central Utility Plant Lock Out Tag Out Procedure.
Electrical Distribution: Any work involving the NC State Electric Distribution System shall follow the requirements specified in the Power Systems Switching Procedure.
Source: https://www.rockfordsystems.com/machine-safeguarding-101/
Approximately 60% of all workplace amputations are caused by machinery, such as saws, presses, conveyors, milling machines, drill stands, bending, rolling or shaping machines, as well as from powered and non-powered hand tools and other materials handling activities.
Understanding the mechanical components of machinery and the hazardous mechanical motion that occurs at or near these components in conjunction with machinery operation and safeguarding is necessary to avoid injury. Safeguarding is essential for protecting employees from injury.
Three types of mechanical components present amputation hazards:
- Point of Operation: Area of the machine where the machine performs work (i.e. mechanical actions that occur at the point of operation, such as cutting, shaping, boring and forming).
- Power-Transmission Apparatus: All components of the mechanical system that transmit energy, such as flywheels, pulleys, belts, chains, couplings, connecting rods, spindles, cams and gears.
- Other Moving Parts: The parts of the machine that move while the machine is operating, such as reciprocating, rotating and transverse moving parts, as well as lead mechanisms and auxiliary parts of the machine.
Key Terms
- Guard: A barrier that prevents exposure to an identified hazard.
- Safeguarding device: A device that detects or prevents inadvertent access to a hazard.
- Awareness device: A barrier, signal or sign that warns individuals of an impending, approaching or present hazard.
- Safeguarding method: Safeguarding implemented to protect individuals from hazards by the physical arrangement of distance, holding, openings, or positioning of the machine or machine production system to ensure that the operator cannot reach the hazard.
- Safe work procedures: Formal written instructions developed by the user which describe how a task is to be performed.
Criteria for Machine Safeguarding
- Prevents employee contact with the hazard area during machine operation.
- Avoids creating additional hazards.
- Is secure, tamper-resistant and durable.
- Avoids interfering with normal operation of the machine.
- Allows for safe lubrication and maintenance.
Types of Primary Safeguarding Devices
- Guards: Physical barrier to prevent access to hazard area. Types: fixed, adjustable, self-adjusting, interlocking shields
- Restraint Devices: Wrists connected by cords and secured to a fixed anchor point to limit hands from reaching the point of operation.
- Presence-Sensing Devices: Interlock into the machine’s control system to stop operation when the sensing field (photoelectric, radio frequency or electromagnetic) is disturbed.
- Presence-Sensing Mats: Interlock into the machine’s control system to stop operation when a predetermined weight is applied to the mat. A manual reset switch must be located outside the protected zone.
- Two-Hand Control: Requires concurrent and continued use of both hands, preventing them from entering the danger area.
- Two-Hand Trip: Requires concurrent use of both hands, prevents them from being in danger area when the machine cycle starts.
Secondary safeguarding methods are acceptable only when guards or safeguarding devices (that prevent you from being exposed to machine hazards) cannot be installed. Where it is feasible to use primary safeguarding methods, secondary safeguarding methods may supplement these primary control measures; however, these secondary safeguarding methods must not be used in place of primary safeguarding methods.
Types of Secondary Safeguarding Devices
- Awareness devices warn employees of an impending, approaching or present hazard.
- Safeguarding methods protect employees from hazards by the physical arrangement of distance, holding, openings or the positioning of the machine components to ensure that the operator cannot reach the hazard.
- Safeguarding by safe distance (by location) may involve an operator holding and supporting a workpiece with both hands at a predetermined minimum safe distance or if both hands cannot be used to hold the workpiece at a distance so that the operator cannot reach the hazard with the free hand.
- Safe Opening Safeguarding limits access to the machine hazardous areas by the size of the opening or by closing off the danger zone access when the workpiece is in place in the machine.
- Safe Work Procedures are formal, written instructions describing how a task is to be performed.
Emergency Stop Devices
Emergency stop devices are designed to be used in reaction to an incident or hazardous situation and, as such, are not considered machine safeguarding. These devices – such as buttons, rope-pulls, cable-pulls or pressure-sensitive body bars – neither detect or prevent employee exposure to machine hazards; rather they initiate an action to stop hazardous motion when an employee recognizes a hazard and activates them.
Train Employees in the Following:
- All hazards in the work area, including machine-specific hazards.
- Machine operating procedures, lockout/tagout procedures and safe work practices.
- Purpose and proper use of machine safeguards.
- All procedures for responding to safeguarding problems, such as immediately reporting unsafe conditions. This includes missing or damaged guards and violations of safe operating practices to supervisors.
Follow safe operating practices, including:
Sling Selection
- Ensure the sling’s rating exceeds the intended load.
- For multiple-leg slings used with non-symmetrical loads, ensure that an analysis by a qualified person is performed to prevent overloading of any leg.
- Ensure that the fitting is the proper shape and size so that it is seated properly in the hook or lifting device.
- Thoroughly inspect all slings prior to and after each use.
Cautions to Personnel
- Ensure that all portions of the human body are kept away from the areas between the sling and the load and between the sling and the crane or hoist hook.
- Ensure personnel never stand in line with or next to the legs of a sling that is under tension.
- Ensure that personnel do not stand or pass under a suspended load.
- Do not use synthetic webbing slings as bridles on suspended personnel platforms.
Effects of Environment
- Store slings in an area where they will not be subjected to extreme temperatures or to mechanical, chemical or ultraviolet damage.
- When slings are exposed to extreme temperatures, follow the guidance provided by the sling manufacturer or qualified person.
- Consult the sling manufacturer for recommended inspection procedures when nylon or polyester webbing slings are extensively exposed to sunlight or ultraviolet light.
Rigging Practices
- Ensure that slings are hitched in a manner providing control of the load.
- Ensure that sharp edges in contact with slings are padded with material of sufficient strength to protect the sling.
- Ensure that slings are shortened or adjusted only by methods approved by the sling manufacturer or a qualified person.
- Ensure that during lifting (with or without a load) personnel are alert for possible snagging.
- Ensure that, in a basket hitch, the load is balanced to prevent slippage.
- When using a basket hitch, ensure that the legs of the sling contain or support the load from the sides and above the center of gravity, so that the load remains under control.
- Do not drag slings on the floor or over abrasive surfaces.
- Ensure that in a choker hitch the choke point is only on the sling body; never on a splice or fitting.
- Ensure that in a choker hitch the angle of choke less than 120 degrees is not used without reducing the rated load.
- Ensure that slings are not constricted, bunched or pinched by the load, hook or any fitting.
- Ensure that the load applied to the hook is centered in the base (bowl) of the hook to prevent point loading on the hook, unless the hook is designed for point loading.
- Do not shorten or lengthen a sling by knotting or twisting.
- Do not rest loads on the sling.
- Do not pull a sling from under a load when the load is resting on the sling.
- Do not allow shock loading.
- Avoid twisting and kinking.
Temperature
Do not allow nylon and polyester slings to be used in contact with objects or at temperatures in excess of 194°F (90°C), or below minus 40°F (minus 40°C).
Sunlight and Ultraviolet
Long-term exposure to sunlight or ultraviolet radiation can affect the strength of synthetic webbing slings. Consult the sling manufacturer for proper retirement criteria for synthetic webbing slings subjected to long-term storage or use in sunlight.
Chemical
The strength of synthetic webbing slings can be degraded by chemically active environments. This includes exposure to chemicals in the form of solids, liquids, vapors or fumes. Consult the manufacturer before using slings in chemically active environments.
IMPORTANT: Many types of mobile equipment have large blind spots and inhibit the operator’s ability to clearly see all around the equipment, as well as a huge swing radius in some cases. Because of this, personnel must be aware of the location and operations of mobile equipment at all times and never assume that the operator sees them. Personnel should not walk directly in the swing radius or in front, back or sides of mobile equipment without first making eye contact with the operator and obtaining approval. The use of a high visibility safety vest is required.
Mobile equipment includes, but is not limited to: UTVs, cranes, front end loaders, dump trucks, mowing equipment, powered industrial trucks, skid steers, garbage trucks, aerial lifts, scissor lifts or other equipment designed to move dirt, material or equipment.
All operators shall be trained and qualified to operate mobile equipment. All mobile equipment shall be operated in compliance with the manufacturer’s instructions, specifications and limitations, as well as any applicable regulations.
Pre-operation inspections must be performed daily each shift by each operator. Inspections must be documented using a proper form or checklist that is applicable to the piece of equipment being inspected. Deficiencies noted during inspection that affect the safe operating condition of the equipment must be resolved before use.
General Guidelines
- Always use safe operating practices including observing the posted speed limit.
- If equipped, seat belt use is required at all times while the equipment is energized.
- Applicable vehicles must have the emergency brake set if the vehicle is parked on a grade.
- All mobile equipment shall be equipped with a functioning back-up alarm audible above the surrounding noise level.
- Personnel are not permitted under any equipment suspended loads unless the equipment/load has been properly blocked and placed in a safe condition.
- Engines shall be shut off and the parking brake engaged during fueling, maintenance operations or when left unattended.
Spotting for Mobile Equipment
A spotter is a person designated to assist the operator in the safe movement of equipment to make sure the heavy equipment does not inadvertently damage people, property and/or equipment/vehicles. Spotters help prevent incidents associated with the movement of heavy equipment. Generally, spotters are required when:
- The operator’s view of the intended path of travel or any part of its travel is obstructed (e.g. reversing, restricted side clearances).
- Operating equipment is in a location in which a person may be endangered by its intended path of travel.
This list is not all inclusive. Operators may identify other situations in which the use of a spotter will help prevent an incident.
WARNING: Spotters are a proven method of reducing incidents involving heavy equipment, but spotters themselves can be at risk for injury or even death. They must receive adequate and effective training to safely do this important task. A safety vest is required at all times when spotting.
Operator Responsibilities
- Identifying when a spotter is required for the movement of equipment.
- Communicating with the spotter and following the spotter’s signals.
- Being aware of their surroundings (e.g. workers adjacent to the equipment).
- Knowing the blind spots of their equipment.
Spotter Responsibilities
- Continuously scanning the area for obstructions and personnel.
- Continuously monitoring the clearances between the equipment and stationary objects.
- Understanding the signals to be used and how to perform them.
- Giving clear and understandable hand signals.

When evaluating your office or remote space for potential hazards, pay attention to the following:
Ergonomics
To avoid musculoskeletal disorders (MSDs), set up your workplaces to provide neutral body positioning. To achieve neutral body positioning, adjust your chair and desk so that your hands, wrists and forearms are straight and parallel to the floor. Then, keep your head level and balanced, your shoulders relaxed and your elbows close to your body. Your knees should be at the same height as your hips and should be parallel to the floor. Your feet should be fully supported by the floor or by a footrest. Request an ergonomic evaluation
Physical Layout
A poor office layout can be distracting, decrease productivity and morale, and put employees at risk for trips, falls, bumps and other injuries. Filing cabinets should be closed when not in use, and cords should be neatly organized where they do not present tripping hazards and are not rolled over by desk chairs.
Lighting
Too much lighting can cause glare on computer screens, which can cause eye fatigue and strain. Employees should not sit with their backs to a window if possible.
Storage
Never store boxes of files, papers or other flammable materials near an ignition source. Stack the heaviest objects or boxes at a height most accessible or on the bottom and the lightest objects on top. Consider securing storage racks to the wall with a wall anchor so they do not tip over. Never store objects in walkways where they could present a tripping hazard. Never store items closer than 24 inches of the ceiling or within 18 inches of a sprinkler head.
Electrical Equipment
Inspect all electrical equipment, such as monitors, fax machines and space heaters, for damaged cords and plugs. Make sure employees are not overloading electrical outlets with multiple power strips or plugging multiple extension cords into each other. Train new and existing employees on what types of electrical equipment are and are not allowed in your workplace.
The primary methods for preventing employee exposure to hazardous materials are elimination, engineering and administrative controls. Where these control methods are not appropriate or sufficient to control the hazard, personal protective equipment (PPE) is required. This may include head protection, eye protection, hand protection, foot protection and respirators.
Use the PPE Hazard Assessment Form to determine required PPE. The form is grouped by the body part requiring PPE.
Eye and Face Protection
Eye and face protection (ANSI Z87) must be worn when exposed to eye and face hazards from flying objects/particles, liquid chemicals, hazardous light radiation or other hazards. Examples of work areas and tasks that require eye and/or face protection include: central utility plants, mechanical rooms, maintenance shops, when using hand and power tools, using and handling chemicals, etc. Eye protection must include side protection. Employees that wear prescription glasses must either use prescription safety eyewear or over the glasses (OTG) safety eyewear.
Head Protection
Head protection (ANSI Z89) is required to be worn when exposed to injury from falling or flying objects or moving equipment.
Hand Protection
Appropriate hand protection is required to be worn when exposed to hazards such as those from cuts or lacerations, abrasions, punctures, chemical burns, thermal burns, absorption of harmful substances and harmful temperature extremes.
Foot Protection
Protective footwear is required in areas where there is a danger of foot injuries due to falling or rolling objects, or objects piercing the sole; or when the use of protective footwear will protect from an electrical hazard.
Respiratory Protection
Employee must be protected from breathing air contaminated with harmful dusts, fogs, fumes, mists, gases, smokes or vapors. When eliminating exposure or controlling with engineering is not feasible, employees must wear appropriate respiratory protection. Employees who wear respirators will be included in the Respiratory Protection Program, which includes medical surveillance, fit testing and training. Employee use of respirators must be approved through NC State Occupational Health. Using filtering facepiece respirators (i.e. N95 ‘dust masks’) is voluntary during activities that involve exposures to nuisance-level particulates; when they are required, all elements of the Respiratory Protection Program apply.
A work area assessment is required to determine the potential hazards and select the appropriate PPE for adequate protection. Employees must receive training that includes the proper PPE for their job; when this PPE must be worn; how to wear, adjust, maintain and discard this equipment; and the limitations of the PPE. All training must be documented.
Resources:
PPE Assessment Form
PPE Considerations
One method for avoiding risks is to identify and communicate known hazards. Safety signs, tags, and barricades play a key role in this. Employees must observe and respect signs, tags and barricades at all times. Failure to do so may lead to injury or death to workers, members of the public or both, as well as property damage.
Signs and Tags
Each sign and tag should include signal word, symbol and text.
Signal Word
- DANGER will almost certainly result in serious injury or death
- WARNING could possibly result in serious injury or death
- CAUTION would not likely result in serious injury or death
- NOTICE indicates important information but not directly hazard-related
- SAFETY INSTRUCTIONS provide explanatory information like procedures and instructions.
Symbols/graphics are used to bridge language barriers and draw attention to a safety message. Specific shapes, colors and designs are used.
Carefully crafted text is used to convey the safety message to the intended audience in a clear, concise manner.
Barricades
A barricade is an obstruction to deter the passage of persons or vehicles. The purpose of the barricade procedure is to reduce the risks of injury to people when a potentially hazardous situation is present.
Barricade Sign
All barricades should be accompanied by a barricade sign, which includes: the name of the person responsible for the barricaded area, method for contacting the responsible person, and clear and concise text describing the purpose of the barricade.
Caution Barricade
Barricading an area where specific potential hazards exist using standard yellow tape with the word “CAUTION” in black letters. Barricades should always have a barricade sign. Authorized persons can enter this area when they are aware of the specific hazard, have taken the necessary precautions to avoid the hazard, and are required to enter the barricade in order to perform work. Persons entering this area should remain in the area no longer than necessary. The caution barricade shall be removed when the hazardous situation has been abated.
Danger Barricade
Barricading an area using standard red tape with the word “DANGER” in black letters should be used for hazards that are immediately dangerous. Barricades should always have a barricade sign. This is used to warn employees of imminent danger and that special precautions are necessary. No one should enter those areas except those authorized to correct the hazard itself. The danger barricade shall be removed as soon as the imminent danger has been abated.
Excavation is any man-made cut, cavity, trench or depression in an earth surface, formed by earth removal. A trench is a narrow excavation (in relation to its length) made below the surface of the ground. The primary hazard of trenching and excavation is cave-in. Other hazards include working with heavy machinery; manual handling of materials; working in proximity to traffic; electrical hazards from overhead and underground power lines; and underground utilities, such as natural gas.
Underground Facilities Locate
Call before you dig so that underground facilities can be identified and avoided. Detailed instructions and requirements can be found at nc811.org.
Competent Person
Trench and excavation work must be performed under the direction of a competent person. A competent person is an individual designated by the employer who is capable of identifying existing and predictable hazards in the surroundings or working conditions and who is authorized to take prompt corrective measures to eliminate them. Responsibilities include: classifying soil, daily inspection of protective systems, monitoring water removal and conducting site inspections.
Cave-In Protective Systems
A protective system is required by OSHA for trenches and excavations that are 5 feet or more in depth OR if the competent person has examined the ground and finds indication of a potential cave-in. Protective systems typically include: sloping/benching, shoring or shielding. In order to determine what protective systems are appropriate, the competent person must first determine the soil type: Stable Rock, Type A, Type B or Type C soil. Type C soil is the least cohesive and therefore, the least stable.
Sloping/Benching
- Sloping: the sides of an excavation can be sloped at specified angles based on the soil type.
- Benching: the sides of an excavation of soil type A or B can be benched (i.e. stepped) at a specified angle of repose; benching is not permitted in type C soils.
Shoring
Shoring is the provision of a support system for trench faces used to prevent movement of soil, underground utilities, roadways and foundations. Shoring or shielding is used when the location or depth of the cut makes sloping back to the maximum allowable slope impractical. Shoring systems consist of posts, wales, struts and sheeting. There are two basic types of shoring: timber and aluminum hydraulic.
Shielding
Shields (Trench Boxes) are different from shoring because, instead of shoring up or otherwise supporting the trench face, they are intended primarily to protect workers from cave-ins and similar incidents. The excavated area between the outside of the trench box and the face of the trench should be as small as possible. The space between the trench boxes and the excavation side are backfilled to prevent lateral movement of the box. Shields may not be subjected to loads exceeding those which the system was designed to withstand. Other general requirements and considerations:
- Excavations >20 feet in depth or which can not comply with OSHA requirements require written approval by a Registered Professional Engineer (RPE).
- A ladder, stairway, ramp or other means of access when excavations are >4 feet in depth.
- No work shall be permitted in excavations where water has accumulated unless the integrity of the excavation has been protected.
- All utilities must have been identified, located and protected as required before excavating.
- Barricades (stop-logs) shall be provided where vehicles or mobile equipment are used near or adjacent to excavations.
- Spoil piles must be placed a minimum of 2 feet from the edge of the excavation.
- Air monitoring must be performed if the excavation is >4 feet in depth and there is a potential for a hazardous atmosphere to exist.
Learn More: OSHA Technical Manual: Excavations
There are certain guidelines that must be followed by all employees who drive university vehicles. Although this is not a complete list of all driving safety requirements, a partial list is outlined below:
- All seatbelt laws must be followed. Seatbelt use is required by law and university policy.
- Posted speed limits, stop signs, stoplights and other posted regulations must be observed while driving a university vehicle or while on university business. These speed limits could be on federal or state roads or highways, as well as site-specific guidelines at a facility. They all must be followed with the same amount of attention. A violation of these posted guidelines leads to an increased risk of mishaps, damage and puts your own safety in jeopardy.
- Avoid driving while distracted. The use of items such as phones, GPS units or other distractions should be avoided while actually driving. Technology affords us the luxury of hands-free phone communication, spoken GPS directions, etc. These safety features should be used or the communication put on hold until after driving has stopped.
It is important to be conscious of all vehicular traffic that may be present during field operations.
- Wear a high visibility safety vest (ANSI Class 2 or 3).
- Use caution tape, barricades, signage or safety cones to denote the boundaries of the work area and to alert vehicle operators to the presence of operations. Cones and signs are only effective if they give oncoming drivers enough time to react and make it clear how traffic should react.
- Use the flashing amber/yellow light located on top of your vehicle to alert traffic to the work zone.
- Be careful when exiting the work area and especially when walking out from between parked vehicles to avoid vehicular traffic. Try to never turn your back to oncoming traffic.
- Arrange work vehicles to be used as a barrier between workers and nearby traffic. If an oncoming car should fail to yield or deviate, the parked vehicle – rather than your body – would absorb the first impact of a crash. Always leave some room between the rear of the vehicle and the work area. Turn the wheels so that if the vehicle were struck, it would swing away from the worksite.
- Employees working on or near public roadways must be trained in accordance with the NC DOT; employees that perform flagging must be trained in accordance with NC DOT authorized programs.
A person is “alone” at work when she or he cannot be seen or heard by another person. Working alone in laboratories, facilities, spaces and other work areas (including fieldwork) is discouraged. This section provides the minimum requirements applicable to all employees and visitors. This procedure is not meant to apply to areas such as offices, conference rooms, break rooms or classrooms where there are no hazardous conditions.
Supervisors must assess activities performed by employees and determine whether they meet criteria of Hazardous Activities or Potentially Hazardous Activities. Activities that fall into either of these categories shall be assigned appropriate hazard controls.
Hazardous Activities or Conditions
Working alone is not permitted. Another person must be in constant attendance within sight and sound who is trained and equipped to react appropriately to an emergency situation.
Hazardous activities and locations are those which present a risk of immediate danger to life or incapacitating injury; therefore, working alone is itself hazardous. Hazardous activities and locations include, but are not limited to the following:
- Working with equipment in which moving machine parts have the potential to cause injuries such as crushed fingers or hands, amputations, entanglement or being pulled into machinery.
- Working on exposed energized electrical conductors, parts or circuits greater than 50 volts AC or DC, which could result in intentional or accidental contact.
- Working with open beam radiation producing devices, high potency biological hazards or chemicals such as pyrophoric, highly flammable, corrosive or acutely toxic chemicals where the concentration, quantity and handling conditions could create a life-threatening condition.
- Changing toxic gas cylinders.
- Entering Permit Required confined spaces.
- Working at elevated heights for which fall protection equipment is required.
- Working over water or in a boat.
Potentially Hazardous Activities
Potentially hazardous activities and locations are those that present the potential for significant injury that might limit a person’s ability to escape the hazard or to self rescue. Examples of potentially hazardous activities and locations include but are not limited to the following:
- Use of chemicals with potential for significant eye injury, inhalation or absorption hazards.
- Working with pressure, vacuum or chemicals with potential for high-energy release.
- Working in a confined space (which does not meet the definition of a permit-required confined space).
- Working where potential exists for exposure to hazardous wildlife or animals that may cause injury.
Acceptable Monitoring Methods
- Having another person within sight or sound who is trained and equipped to respond appropriately to the hazard involved.
- Use of remote monitoring such as continuous camera and/ or audio monitoring.
- Use of a periodic monitoring check-in procedure appropriate to the potential hazard.
- Use of a personal monitoring communication device such as a man-down radio.
Glossary
A
ACGIH – American Conference of Governmental Industrial Hygienists.
ADA – Americans with Disabilities Act.
AIHA – American Industrial Hygiene Association..
ASTM – American Society for Testing and Materials.
Absorption – The process of one substance entering into the structure of another.
Acceptable Air Quality – Air in which there are no known contaminants at harmful concentrations and with which a substantial majority (usually 80 percent) of the people exposed do not express dissatisfaction (ASHRAE 1989-62).
Acute – Effects which are immediately recognizable after an exposure.
Aerosol – An assemblage of small particles, solid or liquid, suspended in air.
Air Cleaning System – A device or combination of devices applied to reduce the concentration of airborne contaminates, such as microorganisms, dust, fumes, respirable particulates, other particulate matter, gases, and /or vapors in the air.
Air Contaminant – An unwanted airborne constituent that my reduce acceptability of the air (ASHRAE 1989-62).
Air Pollutant – An airborne constituent that may adversely affect health.
Allergens – Biological or chemical compounds which if inhaled or if skin contact is made can cause respiratory disorders, skin rashes, eye irritations, etc.
Antimicrobial – Agent that kills microbial growth. See “disinfectant”, “sanitizer”, and “sterilizer”.
B
Biohazard – Any biological organism or product of organisms that presents a risk to human health.
Biological Contaminants – Agents derived from or that are living organisms (e.g., viruses, bacteria, fungi, and mammal and bird antigens) that can be inhaled and can cause many types of health effects including allergic reactions, respiratory disorders, hypersensitivity diseases, and infectious diseases. Also referred to as “microbiologicals” or “microbials”.
Biological safety – A specialized area with the goal of protecting workers from agents of disease, such as bacteria and viruses, by using containment, decontamination and PPE procedures. Also known as “biosafety.”
Bloodborne pathogens – Disease-causing microorganisms present in human blood, including hepatitis B virus (HBV), hepatitis C virus (HCV), human immunodeficiency virus (HIV) and other pathogens.
Building Envelope – Elements of the building, including all external building materials, windows and walls, which enclose the internal space.
Building-Related Illness – Diagnosable illness whose symptoms can be identified and whose cause can be directly attributed to airborne building pollutants (e.g., Legionnaire’s disease, asbestosis, hypersensitivity pneumonitis).
C
CFM – Cubic feet per minute.
CIH – Certified Industrial Hygienist.
CO – Carbon monoxide.
CO2 – Carbon dioxide.
CAS Number—The CAS Number is an identification number assigned by the Chemical Abstracts Service (CAS) of the American Chemical Society. The CAS Number is used in various databases, including Chemical Abstracts, for identification and information retrieval.
Chemical (OSHA)—OSHA’s definition of chemical “means any substance, or mixture of substances.”
Chemical Contaminants – Compounds released from the use of chemicals within a building.
Chronic – Effects which take a long period of time to manifest.
Concentration – The quantity of one constituent dispersed in a defined amount of another.
Confined space “Confined space” means a space that:
- Is large enough and so configured that an employee can bodily enter and perform assigned work
- Has limited or restricted means for entry or exit (for example, tanks, vessels, silos, storage bins, hoppers, vaults, and pits are spaces that may have limited means of entry.)
- Is not designed for continuous employee occupancy.
Contaminant – An unwanted airborne constituent that may reduce acceptability of the air.
D
DOL – Department of Labor. A U.S. cabinet-level department responsible for agencies that oversee safety and health, including the Occupational Safety and Health Administration (OSHA) and the Mine Safety and Health Administration (MSHA)
DOT – Department of Transportation.
Disinfectants – One of three groups of antimicrobials registered by EPA for public health uses. EPA considers an antimicrobial to be a disinfectant when it destroys or irreversibly inactivates infectious or other undesirable organisms, but not necessarily their spores. EPA registers three types of disinfectant products based upon submitted efficacy data: limited, general or broad spectrum and hospital disinfectant.
Dust – An air suspension of particles (aerosol) of any solid material, usually with particle size less than 100 micrometers (µm).
E
EPA – United States Environmental Protection Agency. Oversees U.S. programs that focus on environmental protection, pollution, remediation and programs such as Superfund sites (brownfields).
Emergency preparedness – Includes construction design, food and sanitation equipment storage, as well as conducting drills and preparing a disaster plan.
Employee – A person whose work activities are under the control of an individual or entity; minors and undocumented workers are included in the definition.
Employee assistance program (EAP) – A program contracted by the employer and staffed by psychologists and other health professionals to which employees under stress or exhibiting behaviors that may create an unsafe work environment can be referred.
Employee exposure records – Information, results or records concerning employee exposures to harmful substances or agents in the workplace, such as inventories of chemicals, material safety data sheets and work area sampling results.
Energy Management Control System – Manual and /or automatic control and supervision of the operation of active and passive systems to reduce energy costs.
Ergonomics – Applies science that investigates the impact of people’s physical environment on their health and comfort (e.g., piece of equipment, room or general area).
Exhaust Ventilation – Mechanical removal of air from a portion of a building (e.g., piece of equipment, room or general area).
Exposure – The particular risk factor experienced by the worker, with the specific modifying factors of intensity, time characteristics and duration.
F
FPM – Feet per minute.
Flammable gas (OSHA) – “…means: a gas having a flammable range with air at 20°C (68°F) and a standard pressure of 101.3 kPa (14.7 psi).” ALSO SEE: FLAMMABLE LIMITS, LFL, UFL.
Flammable limits – The range defined by the lower (LFL) and upper (UFL) flammability limit. May sometimes be referred to as explosive limits (LEL & UEL) in other sources of information. This is the range of concentrations in air that may readily ignite when exposed to a flame or spark.
Flammable liquid (OSHA) – “…means any liquid having a flashpoint of not more than 93°C (199.4°F).” ALSO SEE: FLASHPOINT
Flammable solid (OSHA) – “…means a solid which is a readily combustible solid, or which may cause or contribute to fire through friction.”
Flashpoint (OSHA) – “…means the minimum temperature at which a liquid gives off vapor in sufficient concentration to form an ignitable mixture with air near the surface of the liquid, as determined by a method identified in Section B.6.3” of OSHA’s Hazard Communication Standard at 29 CFR 1910.1200. ALSO SEE: FLAMMABLE LIQUID.
Frequency – A measure of how often injuries and illness occur; expressed as a raw number or in some form of rate or ratio.
Fumes – Airborne particles, usually less than 1 micrometer in size, formed by condensation of vapors, sublimation, distillation, calcinations, or chemical reaction.
G
Gas – A state of matter in which substances exist in the form of nonaggregated molecules, and which, within acceptable limits of accuracy, satisfies the ideal gas laws; usually a highly superheated vapor.
Gas Adsorption – Devices used to reduce levels of airborne gaseous compounds by passing the air though materials that extract the gases. The performance of solid sorbents is dependent on the airflow rate concentration of the pollutants, presence of other gases or vapors and other factors.
H
HEPA – High efficiency particulate arrestance (filters).
HVAC – Heating, ventilation, and air conditioning system.
Hazard – A condition with the potential to cause harm or physical damage.
Hazard Communication Standard – The purpose of OSHA’s Hazard Communication Standard, also known as HCS or HazCom, is to address the issue of classifying the potential hazards of chemicals and to ensure that employers and employees can identify and understand hazardous chemicals in the workplace, the physical and health hazards associated with them, and how to take protective action. Hazard communication is achieved by recognition and evaluation of workplace hazards, accurate labeling of hazards, and effective training of employees about proper handling and use of those hazardous materials in the workplace. The OSHA Hazard Communication Standard describes how employers are to inform employees of workplace chemical hazards. The OSHA standard is enforced under the regulations found in 29 CFR 1910.1200.
Hazard not otherwise classified (HNOC) (OSHA) – “Means an adverse physical or health effect identified through an evaluation of scientific evidence during the classification process that does not meet the specified criteria for the physical and health hazard classes addressed in this section. This does not extend coverage to adverse physical and health effects for which there is a hazard class addressed in this section, but the effect either falls below the cut-off value/concentration limit of the hazard class or is under a GHS hazard category that has not been adopted by OSHA (e.g., acute toxicity Category 5).” This definition refers to the Hazard Communication Standard at 29 CFR 1910.1200.
Hazardous chemical (OSHA) – “Means any chemical which is classified as a physical hazard or a health hazard, a simple asphyxiant, combustible dust, pyrophoric gas, or hazard not otherwise classified.” This definition refers to the Hazard Communication Standard at 29 CFR 1910.1200. ALSO SEE: HAZARD COMMUNICATION STANDARD, CLASSIFICATION, HEALTH HAZARD, PHYSICAL HAZARD.
Health hazard (OSHA) – “Means a chemical which is classified as posing one of the following hazardous effects: acute toxicity (any route of exposure); skin corrosion or irritation; serious eye damage or eye irritation; respiratory or skin sensitization; germ cell mutagenicity; carcinogenicity; reproductive toxicity; specific target organ toxicity (single or repeated exposure); or aspiration hazard..” This definition refers to the Hazard Communication Standard at 29 CFR 1910.1200. ALSO SEE: CLASSIFICATION, HAZARD CATEGORY, HAZARD CLASS, HAZARDOUS CHEMICAL
I
IAQ – Indoor air quality. See “Acceptable Air Quality”..
Immediately Dangerous to Life and Health (IDHL) – An atmospheric concentration of any toxic, corrosive, or asphyxiant substance that poses an immediate threat to life, would cause irreversible or delayed adverse health effects or would interfere with an individual’s ability to escape from a dangerous atmosphere.
Imminent hazard – Any condition or practice in a workplace that could cause death or serious physical harm immediately or before the hazard can be eliminated.
Incident – An event, with known casual factors, leading to injury or illness.
Industrial hygiene – A specialized area that recognizes, evaluates and controls chronic (longer-term) worker exposures to harmful physical or chemical agents or conditions such as noise levels, ventilation rates, airborne contaminants, heat exposure and radiation.
Ingestion – Chemicals which enter the body by this route of entry may have local effects and/or may be absorbed into the bloodstream through the small intestine.
Inhalation – Chemicals which enter the body by this route of entry may have local effects and/or may be absorbed into the bloodstream through the lungs.
Inspections – Periodic audits of the workplace environment, including equipment, chemicals, building structure, documented procedures, records and employee knowledge of job requirements and hazards. Interdepartmental or external (conducted by outside agencies) inspections check for compliance with health and safety regulations.
J
Job hazard analysis – This is a process by which a job is studied to determine the hazards involved and ways to safely complete the job by procedures and/or personal protective equipment.
L
Label (OSHA) – “Means an appropriate group of written, printed, or graphic information concerning a hazardous chemical that is affixed to, printed on, or attached to the immediate container of a hazardous chemical, or to the outside packaging.” Containers in the workplace must be labeled in accordance with section (f) of OSHA’s Hazard Communication Standard at 29 CFR 1910.1200
Lanyard – A flexible length of rope, wire or strap used to secure the body, belt or body harness to a deceleration device, lifeline or anchorage.
Light duty – A temporary change in one’s job assignment to accommodate work restrictions.
M
mg/m³ – See “Milligram per Cubic Meter”.
Machine guarding – A device or system that prevents objects from getting caught in the moving parts of machinery.
Material handling equipment – Devices like scissor-lifts, pallet jacks and rolling tables designed to assist in the transport of material.
MSDS – Material Safety Data Sheet – The material safety data sheet has been replaced by the safety data sheet in accordance with OSHA’s 2012 revisions to its Hazard Communication Standard.
Medical surveillance – OSHA requires employers to conduct medical surveillance or evaluations of employees who are exposed to certain chemicals or other hazardous substances to assure that chemical or substance exposure is within the acceptable limits or has not caused harm.
Microorganism – A microscopic organism especially a bacterium, fungus or a protozoan. See “Biological Contaminants”.
Milligram per Cubic Meter – The concentration of a chemical compound in milligrams per cubic meter of air.
Mine Safety and Health Administration (MSHA) – An agency of the Department of Labor that oversees surface and subsurface mining safety rules and regulations. MSHA conducts inspections, assists with training, and can issue citations, penalties and-cease-and-desist orders in situations where a mine’s practices create imminent danger to workers.
Multiple Chemical Sensitivity – A team used by some people to refer to a condition in which a person is considered to be sensitive to a number of chemicals at very low concentrations. There are a number of views about the existence, potential causes and possible remedial action regarding this phenomenon.
N
NFPA – National Fire Protection Association. NFPA is a non-profit organization which provides information on fire protection and prevention. Among the publications the NFPA develops is the 704 Standard for the Identification of the Fire Hazards of Materials. This publication describes a hazard warning system suitable for labels on containers. See www.nfpa.org.
NIOSH – National Institute for Occupational Safety and Health – National Institute for Occupational Safety and Health. NIOSH is involved in research on health effects due to workplace exposures. Research is used to make recommendations for reducing or preventing worker exposures. NIOSH is also responsible for testing and certifying respirators. See www.cdc.gov/niosh.
Negative Pressure – Condition that exists when less air is supplied to a space than is exhausted from the space so the air pressure within the space is less than that in surrounding areas.
O
OSHA – Occupational Safety and Health Administration.
Occupational Health Physician – Board certified physician trained in regulation, evaluation and treatment of occupational disease/injuries.
Odor – A quality of gases, liquids or particles that stimulates the olfactory organ.
Oxidation – A reaction in which oxygen combines with another substance.
P
P.E. – Professional Engineer.
PELs – Permissible Exposure Limits (standards set by OSHA). The PEL refers to the maximum air contaminant concentration a worker can be exposed on a repeated basis without developing adverse effects. The PELs are listed in 29 CFR 1910.1000 Tables Z-1, Z-2, Z-3. ALSO SEE: CFR 29 Section 1910 Subpart Z.
PM – Preventative Maintenance.
PPM – See “Parts Per Million”.
PSI – Pounds per square inch.
Particulate Matter – A state of matter in which solid or liquid substances exist in the form of aggregated molecules or particles. Airborne particulate matter is typically in the size range of 0.01 to 100 micrometers.
Parts Per Million – A concentration which expresses the amount of a chemical contaminant (parts) of air or water.
Personal protective equipment (PPE) – Equipment worn or used by workers to protect themselves from exposure to hazardous materials or conditions. The major types of PPE include respirators, eye protection, ear protection, gloves, hard hats and protective suits.
Positive Pressure – Condition that exists when more air is supplied to a space than is exhausted, so the air pressure within that space is greater than in surrounding areas.
R
RELs – Recommended Exposure Limits (recommendations made by NIOSH).
Relative Humidity (RH) – The relative difference between the amount of water vapor in the air and temperature. If water vapor remains the same, RH will decrease as temperature increases because warmer air can hold more water.
Respirator use – Respirators are commonly used to protect workers from hazardous vapors and gases and particulates. There are respirators that remove hazards and those which supply the worker with air. Each type has limitations and advantages. Proper selection and use is essential to worker health. OSHA and ANSI provide guidance for respirator use
Rhinitis – Eye irritation.
Right to Know law – This is a term applied to a variety of laws and regulations enacted by municipal, county and state governments that provides for the availability of information on chemical hazards. This also includes the OSHA Hazard Communication Standard. The different laws that have been enacted around the country vary greatly from the OSHA Standard. Some require that information be made available not only to employees, but to emergency personnel and the community as a whole. Many of the local and state laws require submission of work area surveys as well as annual activity reports. The basic intent of these laws is the same as the OSHA Standard. ALSO SEE: HAZARD COMMUNICATION.
S
SBS – See “Sick Building Syndrome”.
SDS (OSHA) – “Means written or printed material concerning a hazardous chemical that is prepared in accordance with paragraph (g) of” OSHA’s Hazard Communication Standard at 29 CFR 1910.1200. Safety data sheets have a specified 16-section format that chemical manufacturers, importers, and other employers responsible for preparing SDSs must follow as of June 1, 2015.
STEL – Short Term Exposure Limit. This is a term used by the ACGIH to denote “a 15-minute time-weighted average exposure which should not be exceeded at any time during a work day even if the eight hour time-weighted average is within the TLV.” As with the TWA-TLV, the STEL is only a recommendation. ALSO SEE: TLV, TWA.
Safety data sheet (OSHA) – See SDS.
Safety talk meetings – Short on-the-job meetings in heavy industry and construction to keep employees apprised of work-related hazards.
Sanitizer – One of the three groups antimicrobials registers by EPA for public health issues. EPA considers an antimicrobial to be a sanitizer when it reduces but does no necessarily eliminate all the microorganisms on a related surface. To be a registered sanitizer, the test results for a product must show a reduction of at least 99.9% in the number of each test microorganism over the parallel control.
Short Term Exposure Limit – SEE STEL
Sick Building Syndrome – Term sometimes used to describe situations in which building occupants experience acute health and/or comfort effects that appear to be linked to time spent in a particular building, but where no specific illness or cause can be identified. The complaints may be localized in a particular room or ozone, or may be spread throughout the building.
Sterilizer – One of the three groups of antimicrobials registered by EPA for public health issues. EPA considers an antimicrobial to be a sterilizer when it destroys or eliminates all forms of bacteria, fungi, viruses, and their spores. Because spores are considered the most difficult form of a microorganism to destroy, EPA considers the term sporicide to be synonymous with “sterilizer.”
Substance (OSHA) – “Means chemical elements and their compounds in the natural state or obtained by any production process, including any additive necessary to preserve the stability of the product and any impurities deriving from the process used, but excluding any solvent which may be separated without affecting the stability of the substance or changing its composition.” This definition refers to OSHA’s Hazard Communication Standard at 29 CFR 1910.1200.
Supervisors – Those persons who have the authority to direct the tasks of other employees and who are therefore responsible for the job-related environments to which their workers are exposed. Supervisors may also be required to develop local area procedures, train workers in health and safety, enforce rules and maintain records.
T
TLVs – Threshold Limit Values (guidelines recommended by AVGIH). The TLVs are a group of recommended concentrations established by the ACGIH for worker protection. They are based on toxicity data generated from human and animal studies and industrial experience. TLVs are only recommendations to industry, whereas OSHA enforces the PELs. ALSO SEE: TWA, Ceiling, STEL, Skin notation, PEL, ACGIH.
TVOCs – Total Volatile Organic Compounds.
U
V
VOCs – See “Volatile Organic Compounds”.
Vapor density – This is the comparison of the density of a vapor or gas to the density of air (air = 1). A vapor density of less than 1 means it is lighter than air, and greater than 1 means it is heavier than air. Toluene has a vapor density of 3.14.
Vapor pressure – A measure of the volatility of a liquid, usually given in millimeters of mercury (mmHg). The vapor pressure of toluene at 68°F is 22 mmHg and 760 mmHg at 231°F (the boiling point).
Ventilation – The process of supplying and removing air by natural or mechanical means to and from any space. Such air may or may not be conditioned (ASHRAE 62).
Volatile Organic Compounds (VOCs) – Compounds that evaporate from the many housekeeping, maintenance, and building products made with organic chemicals. These compounds are released from products that are being used and that air in storage. In sufficient quantities, VOCs can cause eye, nose and throat irritation, headaches, dizziness, visual disorders, memory impairment; some are known to cause cancer in animals; some are suspected of causing cancer in animals; some are suspected of causing, or are known to cause cancer in humans. At present, not much is known about what health effects occur at the levels of VOCs typically found in public and commercial buildings.
W
WHO – World Health Organization.
Water-reactive (OSHA) – “Means a chemical that reacts with water to release a gas that is either flammable or presents a health hazard.”
Workplace (OSHA) – “Means an establishment, job site, or project, at one geographical location containing one or more work areas.”
Z
Zone – A space of group of spaces within a building with similar heating or cooling requirements that can be maintained throughout by a single controlling device system.